Introduction
Corrosion is almost always a destructive force that, when not carefully attended to, may significantly impact the lifespan, strength, and integrity of industrial machines, pipelines, bridges, automobiles, and other infrastructural amenities.
Corrosion may have very serious consequences expensive servicing and a high rate of maintenance, or it can even be dangerous. Such corrosion-resistant coatings provide a highly effective solution to these issues, offering protection that not only extends an asset's life but also reduces long-term maintenance costs.
In this blog, we will delve into the importance of corrosion-resistant coatings, explore how they work, and discuss their key applications across different industries.
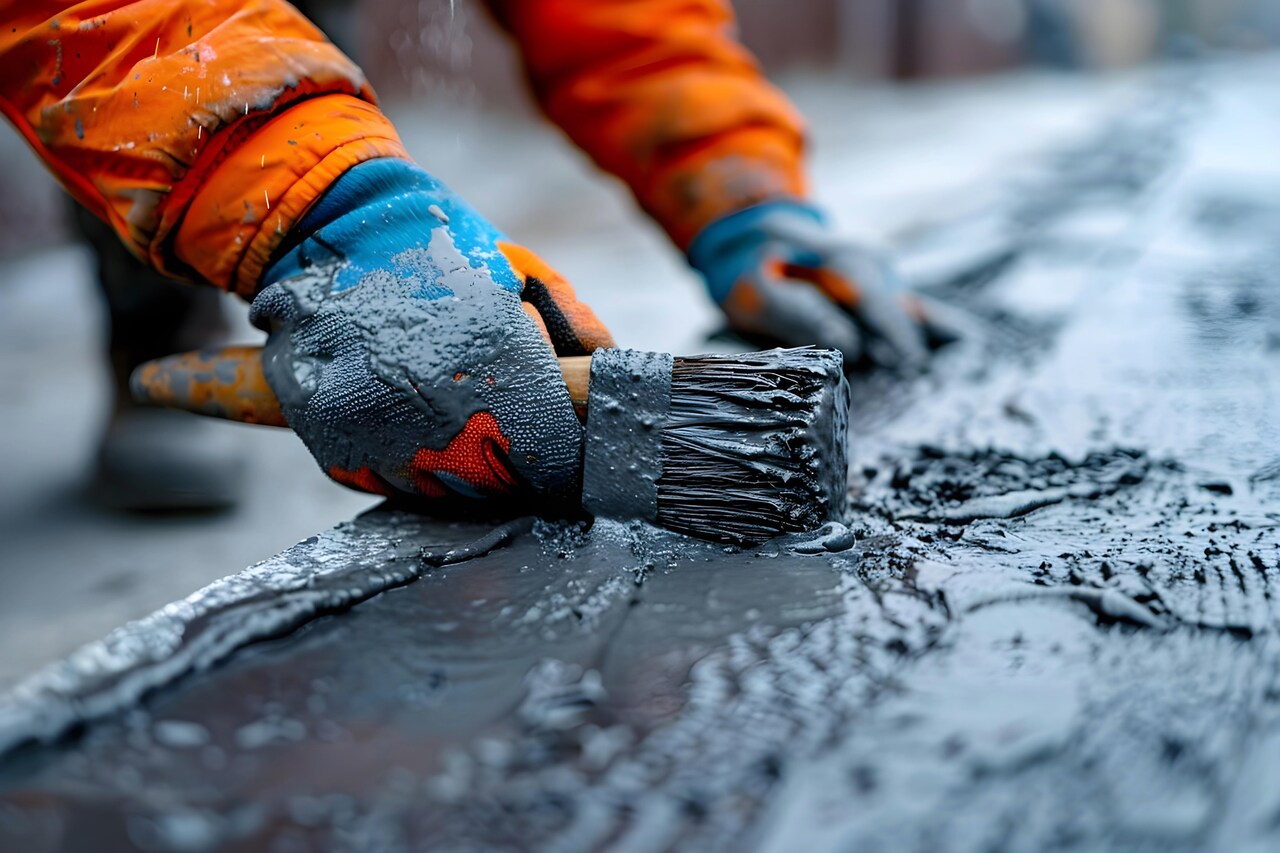
Understanding Corrosion and Its Impact
Corrosion is the natural process of metal deterioration due to the chemical reaction with elements in the environment on which it is situated – moisture, oxygen, and others. The reaction makes the material weak, and therefore structural integrity of the parts affected is threatened.
The most common kind of corrosion is oxidation. Iron, upon reacting with oxygen and water, will turn into iron oxide, more commonly referred to as rust.
However, the problem of corrosion is not just aesthetic but also serious for safety, performance, and the financial side of any project. Corroded metals become brittle and can easily be broken.
Risk problems that could result from corrosion are a key area of concern in the construction, manufacturing, transportation, and energy industries.
An oil and gas pipeline, for instance, that leaks its content due to corrosion, can bring about environmental damage or, in some cases when it fails catastrophically; on the other hand, rusting machinery can bring about operational downtime, which is very costly in terms of repair.
What Is Corrosion-Resistant Coatings?
Corrosion-resistant coatings are materials specially formulated to either prevent the corrosion process or at least slow it down, primarily by acting as a barrier between the metal, its environment, and a corrosive medium.
Such coatings are designed using a specific formulation that protects the metal's surface from extremely harsh environmental conditions that otherwise lead to corrosion.
There are all manner of corrosion-resistant coatings available for specific applications and environmental conditions. The coatings protect against corrosion and improve durability and performance on coated surfaces by safely ensuring service and function over their extended life span.
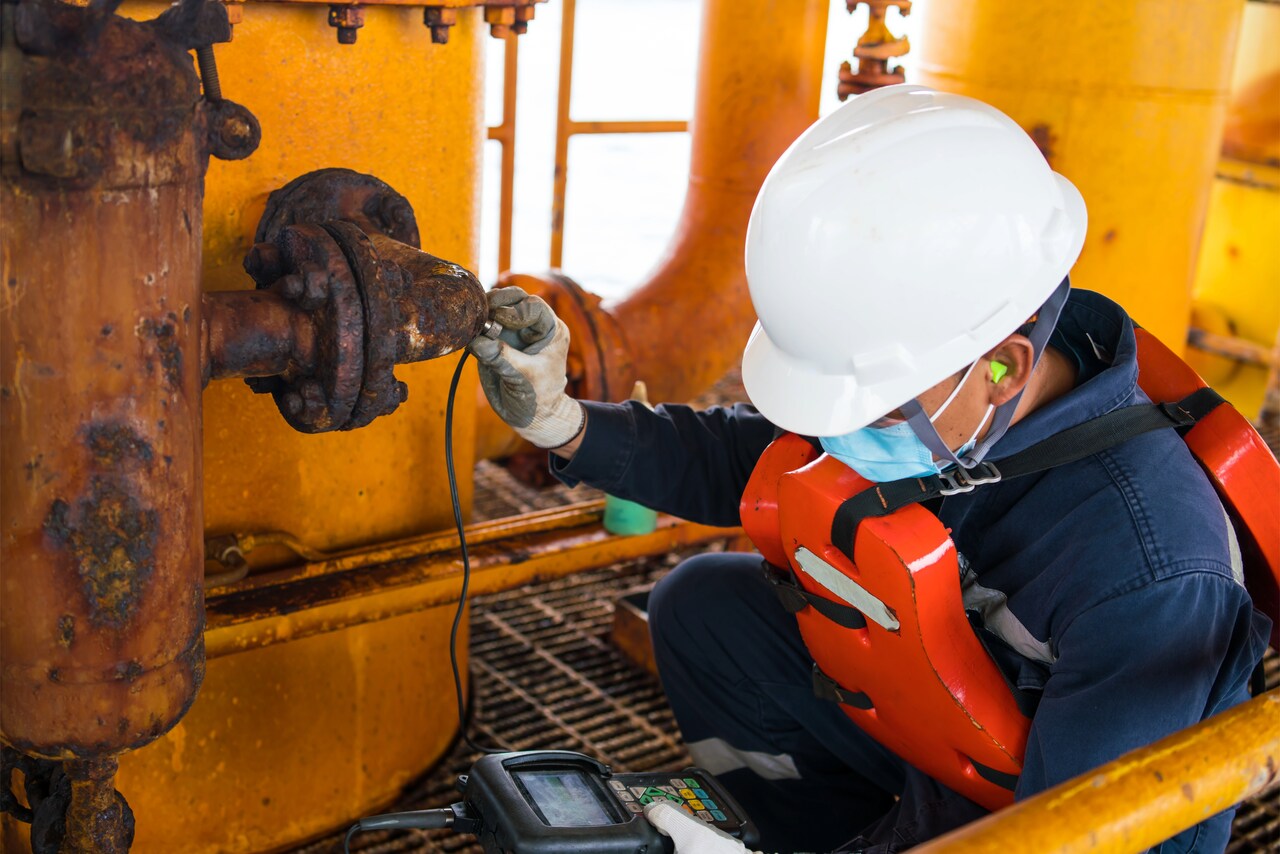
Benefits of Corrosion-Resistant Coatings
Few benefits of Corrosion-Resistant Coatings include:
- Extended Asset Lifespan: The major benefits of corrosion-resistant coatings are that they extend the life of metallic components and structures for a very long. By preventing corrosion there is no need for ongoing repair regularity or replacing units of components, which at the end of the day saves the company thousands if not millions in the long run.
- Reduced Maintenance Costs: Frequent maintenance to control corrosion costs much money and people's time. Corrosion-resistant coatings reduce the need for continual maintenance, which consumes much time and prevents labor charges for the same. Thus, they assist in reducing the production losses that would result from downtime to carry out repairs or replacements for corroded portions.
- Enhanced Safety: These are safety hazards of the highest order, especially with critical industries like oil and gas, transportation, and construction. The corrosion-resistant coatings ensure that a company's structures, machines, and even vehicles are safe and capable of being relied on for the intended work, as they will not easily succumb to accidents or failure.
- Improved Aesthetics: Further, these coatings are aesthetic in that they enhance the general appearance of metals. The prevention of rust or any other corrosive element maintains cleanliness and professionalism, particularly in commercial and customer-related uses.
- Environmental Protection: Corrosion-resistant coatings can help to protect the environment by eliminating the need for harsh chemical treatments and reducing waste from corroded materials. Some coatings are specifically designed with compliance in mind, with the help of environmentally friendly formulations that are non-toxic and renewable to further reduce their environmental impact.
- Compliance with Industry Standards: Many industries have strict rules for corrosion protection. Corrosion-resistant coatings allow these businesses to follow the standards put in place by various industries for their products while avoiding punitive fines, litigation, and damage to their reputation.
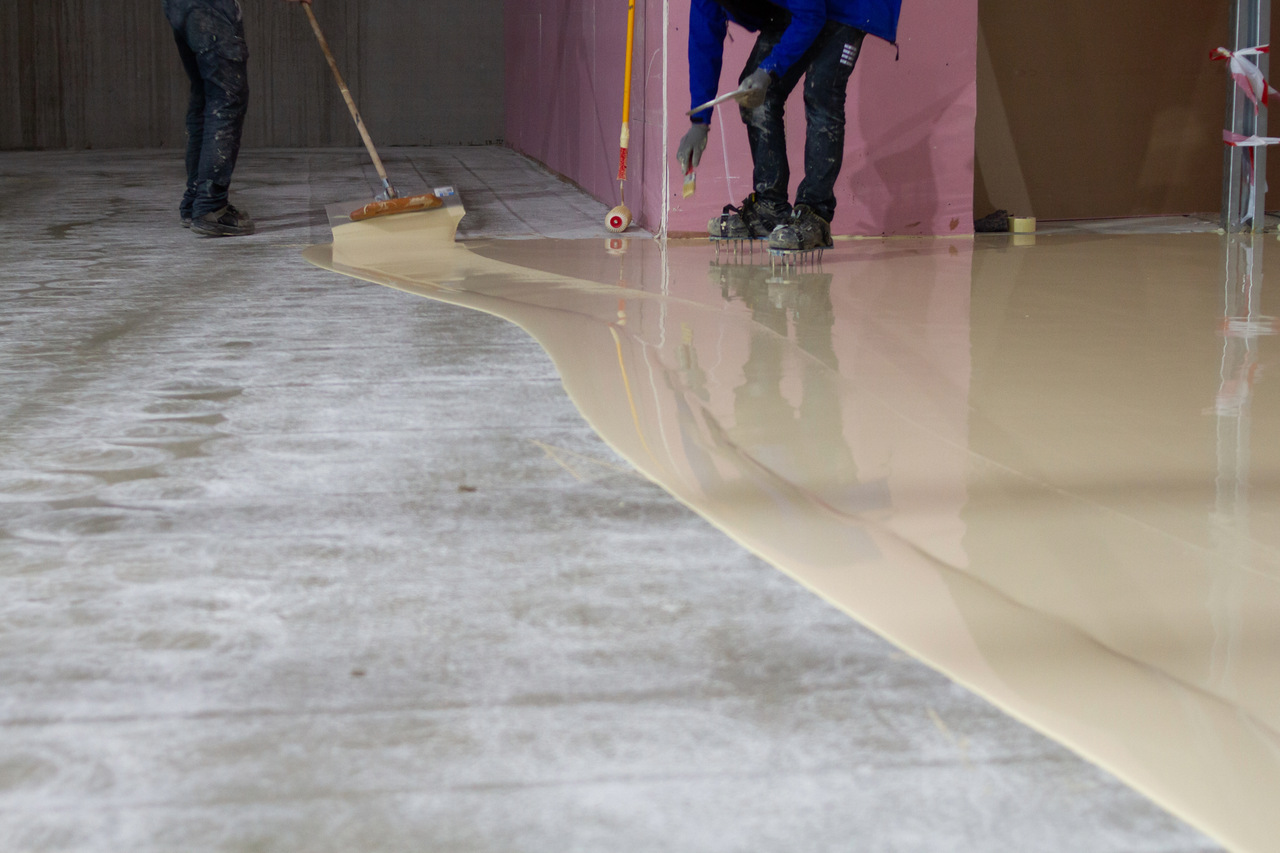
Types of Corrosion-Resistant Coatings
There are several types of corrosion-resistant coatings, each offering distinct advantages depending on the application and environmental conditions:
1. Epoxy Coatings
Epoxy coatings dominate because of their superior qualities of adhesion, toughness, and resistance to humidity, chemicals, and abrasion. Epoxy coatings on steel, concrete, and other industrial construction materials remain, by large, the only way to protect these products over their lifetime in aggressive hostile environments.
2. Polyurethane Coatings
Polyurethane coatings are high-levels of performance, abrasion-resistant coatings that resist UV radiation and weathering for use over continuously exposed steel outside, for example, in bridges, buildings, or vehicles. The coatings are also applied in areas of dynamic surface activities because they are flexible and tough.
3. Zinc Coatings (Galvanization)
Galvanization refers to the coating process for steel or iron with a sacrificial layer of zinc. Zinc corrodes instead of the actual metal beneath, offering enough protection for rusting to be avoided. This explains its growing use in building, automobile manufacturing, and marine industries where protection against corrosion is frequently required in seriously corrosive environments.
4. Powder Coatings
The powder coatings are added as a dry powder, and then they cure under heat. In other words, they provide very good protection against chipping, scratching, and corrosion, so they are used for home appliances, car spare parts, and even outdoor furniture.
5. Ceramic Coatings
Ceramic coatings are commonly applied to resist high temperatures, abrasions, and chemical corrosion. These types of coatings are applied in many aerospace, automotive, and industrial purposes, which face high temperatures and hostile situations.
6. Fluoropolymer Coatings
Fluoropolymer coatings Other than being abrasion-resistant, they show exceptionally good chemical resistance and low friction, making such coatings very relevant for use in chemical processes, food processing, and pharmaceutical industries. These coatings work very well with environments that pose exposure to aggressive chemicals.
7. Alkyd Coatings
Alkyd coatings are oil-based and work well in many applications where water and chemical resistance are needed. That explains why they flooded marine environments and exterior structures where contact with moisture and rough conditions was a common phenomenon.
Applications of Corrosion-Resistant Coatings
Corrosion-resistant coatings are essential across a wide range of industries and applications:
1. Oil and Gas Industry
This is because the pipelines, offshore platforms, and storage tanks in this industry are exposed to very aggressive environments that may trigger rapid corrosion. The coatings protect the assets from saltwater, chemicals, and extreme temperatures in the natural surroundings, thus enabling their longevity and safety.
2. Construction
Antirust helps avoid the rust of structural steels until it's ready to serve its effective period according to the design life. Structures in coastal and industrial areas, where the corrosion action is at a higher level than usual, may need rejuvenation or renewal of the corrosion-resistant materials after a fixed period.
3. Marine Industry
All such marine vessels are mostly in contact with saltwater, and hence the risk of corrosion is very high. The antirust coatings protect the hulls, decks, and other metals on the vessels from rusting or deteriorating so that they remain fit to survive for a long time and stay as well.
4. Automotive Industry
Exposed to water, salt, and chemicals, among many other corrosive materials, vehicles may therefore suffer some pitfalls of corrosion. Corrosion-resistant coatings put on the body, and underbody among many other parts of the vehicles protect these vehicles from rust hence making them alive with a great appearance while extending their life.
5. Industrial Equipment
Equipment and heavy machinery used in manufacturing, mining, and other industrial ventures are often in contact with aggressive media, among very many other extreme conditions. Therefore, corrosion-resistant coatings preserve equipment for use in these sectors and lead to a reduction in the cost of maintenance and downtime in these sectors.
6. Infrastructure
Public infrastructure such as bridges, tunnels, and pipelines are constantly exposed to the elements and high usage rates. Corrosion-resistant coatings preserve these structures, ensuring their safety and preventing costly repairs and replacements.
Choosing the Right Corrosion-Resistant Coating
Selecting the appropriate corrosion-resistant coating involves considering several factors:
1. Environmental Conditions
Consider the environment in which the coated surface will be used. An example is marine coatings must bear saltwater, whereas industrial coatings may be required to bear chemicals and high temperatures.
2. Material Compatibility
Make sure that the coating is compatible with the substrate material whether steel, aluminum, concrete, or the like. The wrong coating can result in significant adhesion problems and lower performance.
3. Application Method
Methods of application may be different depending on the nature of the coating, and some general methods include spraying or brushing and, on the other hand, dipping. Select a coating that can be applied well and economically for your application; the environmental conditions could be either known or purely hypothetical.
4. Durability and Longevity
Review and evaluate the durability of the coating, or more vitally, how long it can give the protection. Some coatings offer protection for long periods, while others must be maintained frequently, and others reapply after time elapses. It should therefore be taken into consideration how the coating would perform over time and if it would be able to bear up under the conditions to which it is to be exposed.
5. Cost
The initial cost of coatings with good corrosion resistance is high, but usually, long-term benefits in terms of asset life expansion and minimized maintenance overtake such costs. Look at the total ownership cost by considering application and maintenance costs and potential long-term savings from a downtime and repair reduction.
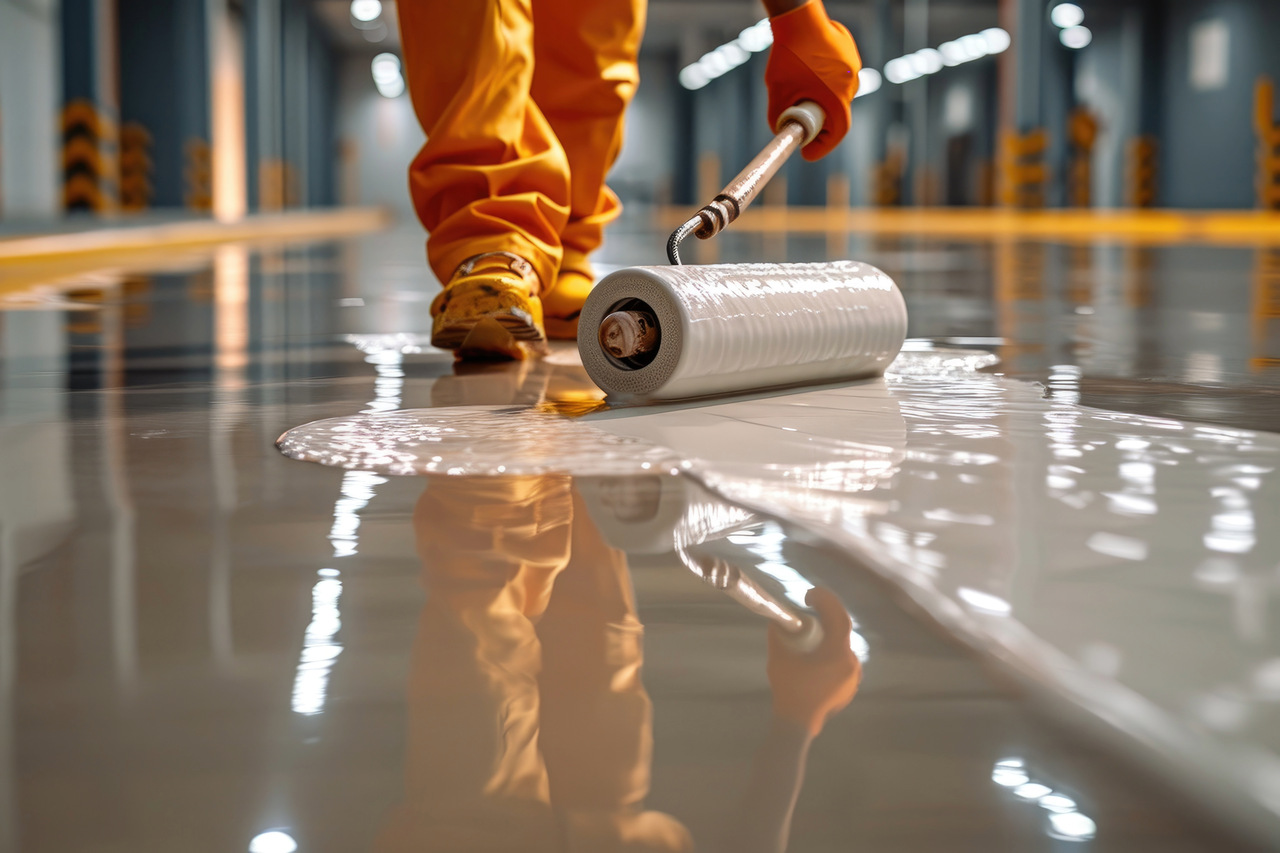
Advancements in Corrosion-Resistant Coatings
Recent advancements in corrosion-resistant coatings have significantly enhanced their performance, offering new levels of protection in even the most challenging environments. These innovations include:
1. Nanotechnology-Based Coatings
Nanotechnology will form the backbone of new coatings that are considered to improve protective properties. Nano-coatings contain ultra-fine particles compared to the size of particles in traditional coatings, therefore they can build a protective layer that is denser and more homogeneous. This results in improved corrosion resistance and enhances mechanical properties like hardness and flexibility.
2. Self-Healing Coatings
A breakthrough in corrosion protection: self-healing coatings are incorporated with microcapsules in which a healing agent is stored. The agent is released from the capsules when the coating is broken, reacting with the outside environment to form a protective barrier against corrosion on the damaged area.
3. Eco-Friendly Coatings
And with environmental issues taking the front seat, there was also an increment in the demand for environmentally friendly coatings. The coatings are formulated from nontoxic materials that are biodegradable and therefore do not affect the environment much in case of corrosion protection. On the other hand, besides being more environmentally friendly ecological coatings also meet the highly strict regulatory impositions on reducing the use of hazardous substances.
Case Studies: Successful Applications
1. Offshore Oil Platform
An offshore oil platform in a very aggressive marine environment had an unusually fast degradation of structural members exposed to saltwater, together with several aggressive chemicals, daily.
The high-performance epoxy coating greatly decreased the process of corrosion of the platform, thus expanding the useful life of the same, with minimized costs for periodic maintenance, and improving safety by considerably lowering the potential for any structural failures of the platform.
2. Automotive Manufacturer
A very large automotive manufacturer was facing a problem. Corrosion on the underbody of their vehicles was leading to complaints by customers and higher levels of warranty claims.
So, the company began applying a zinc-rich primer and a polyurethane topcoat. Along with contributing excellent protection against corrosion, this did not affect the aesthetic appearance of the coated article. In simple words, the company reduced corrosion and enhanced customer satisfaction at the same time.
3. Public Infrastructure
Most of these deteriorating bridges and tunnels are highly corroded within such a gigantic network and very expensive to rectify. The city government chose sensitive areas where it could use epoxy and polyurethane combinations to give them a longer lease of life.
This proactive policy saved the city millions in repairs and extended infrastructure life. In addition, the durability effect led to increased maintenance intervals, which in a way lowered the maintenance, expensive in the long run.
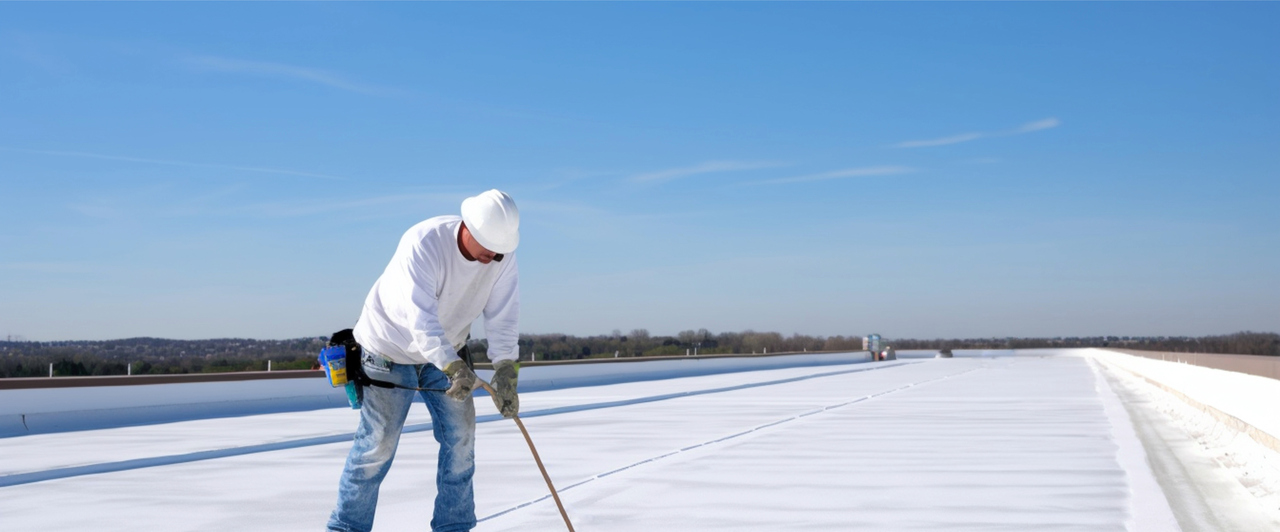
Application and Maintenance of Corrosion-Resistant Coatings
Proper application and maintenance are key to ensuring the effectiveness of corrosion-resistant coatings:
Step 1: Surface Preparation
The surface must be free of previous contamination, dry, and clean for coating application. This can be done through sandblasting or cleaning by solvents or primers to ensure proper adhesion. Poor surface preparation will transfer into a failed coating with reduced protective ability.
Step 2: Coating Application
The recommended thickness of the coating should be followed, and it should be applied as per the manufacturer's instructions to achieve the right coverage. Multiple coats may have to be applied to achieve maximum protection. The application method in the form of spraying, brushing, or dipping must be done according to the type of coating and the requirements of the project.
Step 3: Drying and Curing
Allow the coating to dry and set fully before it gets exposed to corrosive environments. Both drying and curing times are based on the coating type, environmental conditions, and thickness of the coat to which it is applied. Proper curing must be provided to make use of the potential protective ability of a coat.
Step 4: Regular Inspections
These coated surfaces should be inspected regularly for any signs of wear out, damage, or corrosion. Any anomalies detected in such inspections shall be repaired by touching up or re-coating a surface, as needed. Such inspections will help keep up the effectiveness of a coating and thereby prolong the life of protected assets.
Conclusion
In essence, corrosion-resistant coatings form a very good investment toward protecting any given metal structure and equipment against the destructive action of corrosion.
Over the long term, they furnish the best value by maintaining assets longer, reducing maintenance costs, and enhancing safety in the industry. In construction, manufacturing, or transportation, and in almost every industry where corrosion may be a problem, the right coating, applied correctly, will make a major impact on the investment in question.
It invests in protection against corrosion for metal structures and equipment and the fauna and flora surrounding a process plant. Coatings add life to an asset, save on maintenance, and contribute to improving safety, thereby ensuring outstanding value in the long run for all industrial activities be they related to construction, manufacturing, transportation, or any other type of industrial activity related to the corrosion phenomenon.
Your investment could be best protected with an application of proper type coating by wiser selection and its adequate application.
However, application mode, material compatibility, and environmental conditions must be considered when selecting a corrosion-resistant coating to optimize protection.
Furthermore, sufficient maintenance and routine inspections are required to maximize its performance over its service life. Proper management of a proactive corrosion protection strategy will prevent expensive damage through promoting safety for your assets and realization of long-term savings.